In Mold Labeling
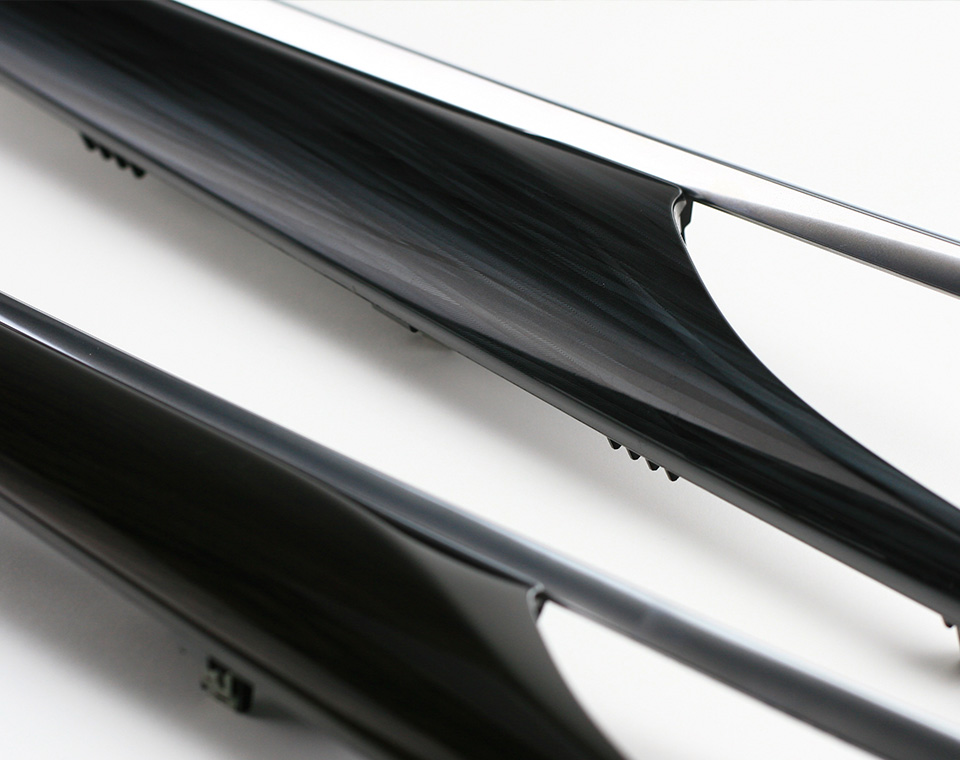
IML = In Mold Labeling is the technology to apply printed and pre-formed film onto 3D geometry plastic surface where film and plastic are adhered during injection molding.
This technology is especially suitable for decorating deep and complex shape. Furthermore, because of surface IML film layer, a high-quality exterior with a sense of depth and robust physical properties are available.
Key benefits
Complex curved geometry available
Dedicated forming process prior to injection molding forms IML film deep draw and complicated geometry.
IML film layer protection
Graphic layer is fully protected from abrasion by IML film. Additional functionalities like UV or chemical resistance is available by special films.
Environmental friendly
Thin IML ink is only applied to the area where decoration is needed. Volatile organic compounds can be reduced.
Production lot flexibility
Nissha range of printing methods allows flexible manufacturing. Silk-screen printing for lower volume production, Gravure printing for higher volume production.
Versatile surface finish
Unique coating and printing technology can create excellent natural finishes including tactile texture, effects like stainless steel, natural wood, and fabric-like patterns.
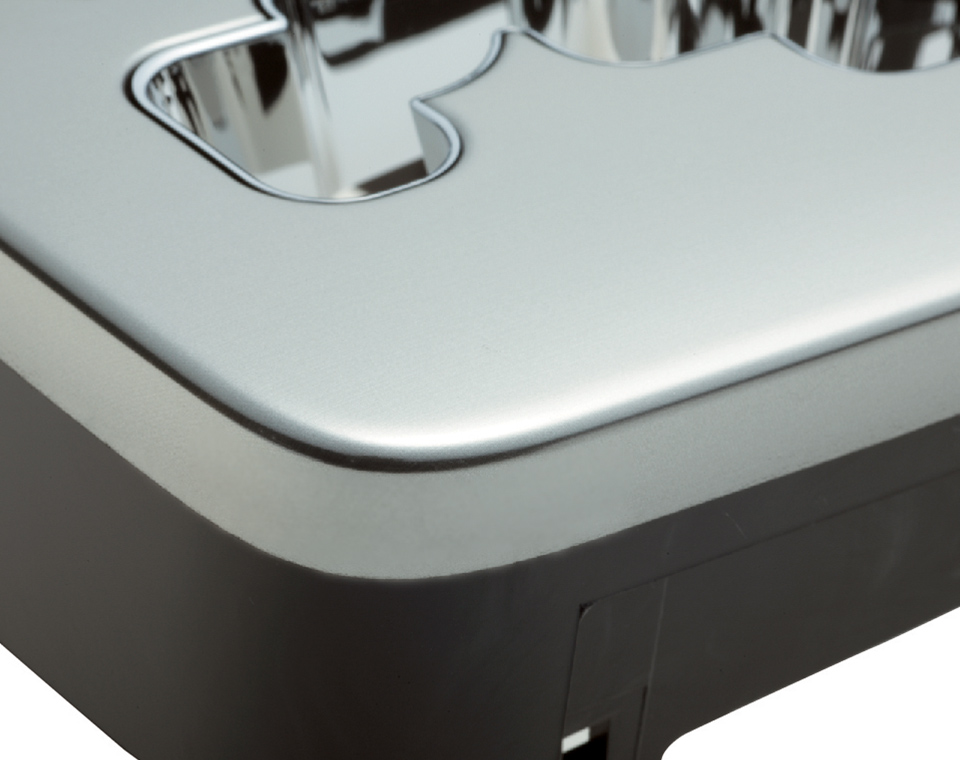
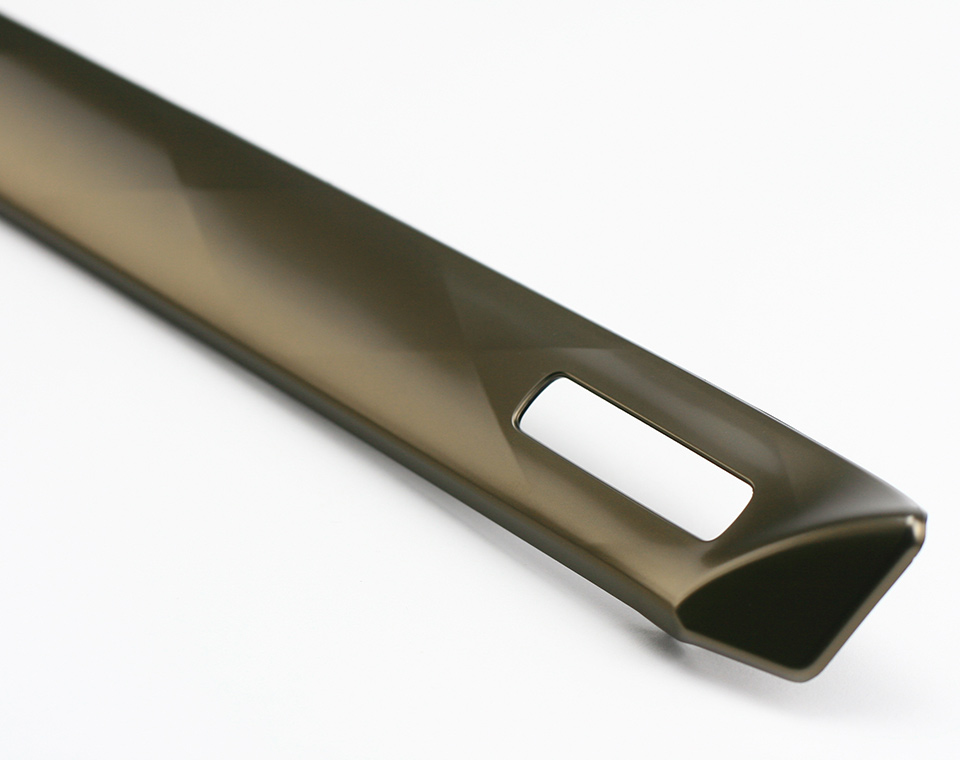
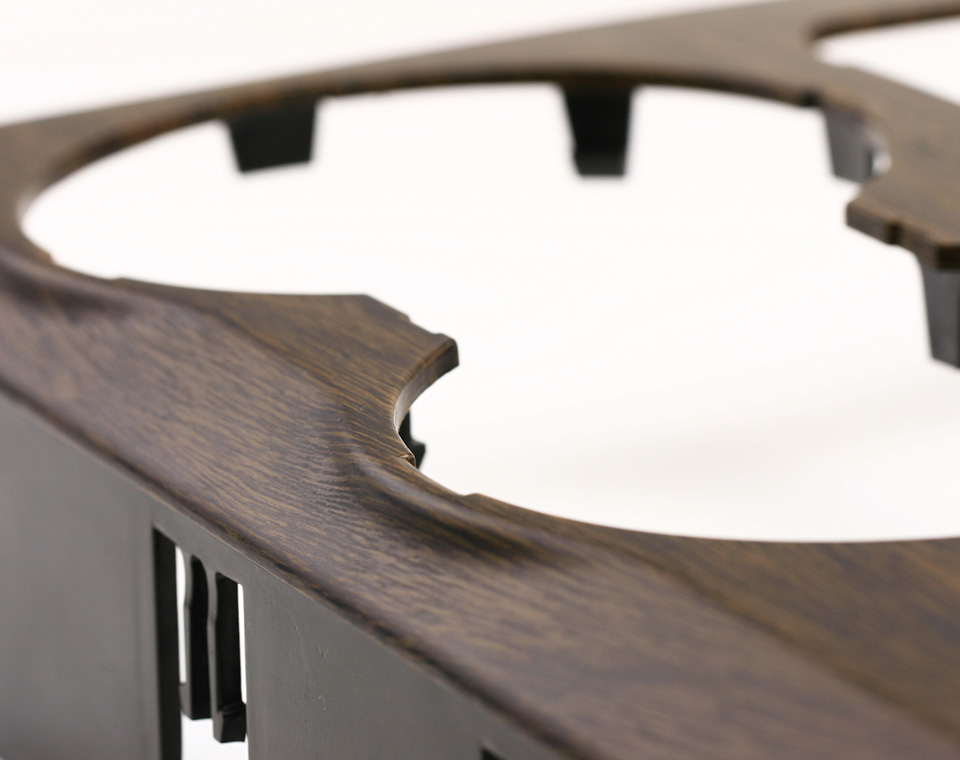
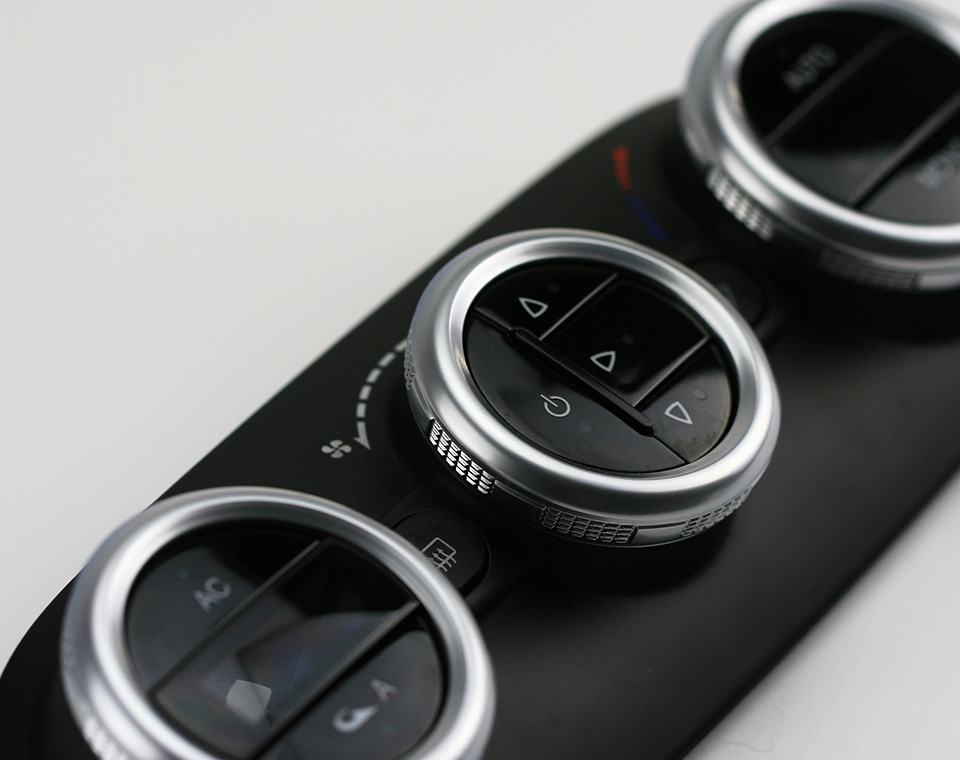
Process
IML process consists of multiple steps – printing, forming, trimming and molding.
Because of the dedicated forming process, IML process is well suited for deeper draw parts and complicated geometries.
Also, since the carrier film remains on the surface with the IML process, a high-quality exterior with excellent physical properties and a sense of depth can be achieved.
Composition
Process Flow
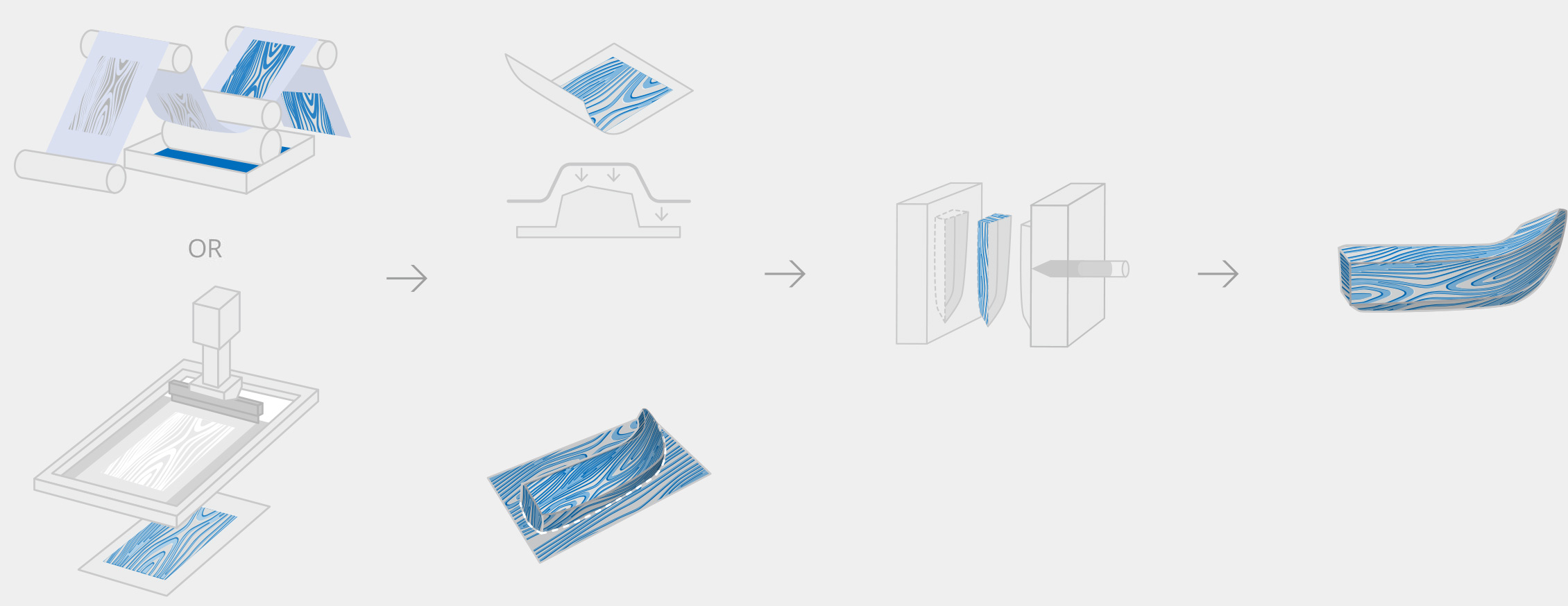
Printing
For IML film, Nissha has two printing methods – Gravure printing and Silk screen printing. Depending on design specification and production volume, the best printing method is chosen.
Forming and Trimming
IML film is set in the forming machine and formed into the geometry of the part’s shape by high heat or high pressure. Then the periphery film is trimmed by die cut machine or laser.
IML molding
Formed IML film is inserted into the injection molding tool and combined with resin.
Product
After injection molding, the result is finished decorated products.
Comparison between IMD and IML
Layer structure
IMD
IML
Film
Released
Remain
Remain
Roll to Roll
Sheet
Process
Simple (Just Molding)
Multiple (Forming / Trimming / Molding)
Geometry
Shallow
Flexible (Sharp, Deep)
Volume
Middle – High volume
Low – Middle volume
Nissha Type-P system for Automotive industry
“Type-P” system, one of IML technology of Nissha, is optimized technology for automotive industry. Type-P film is composed 2 layers of film, PMMA film as surface and ABS film for backer. Total thickness of film is about 0.5mm. This specific film structure allows strong durability and stretching for deep draw geometry which are required in automotive industry.
Also, Nissha have another IML system, call “Type-S”. This is roll to roll process and forming and trimming was done inside of tooling. If you are interested in our variety of IML solution, please feel free to contact us.
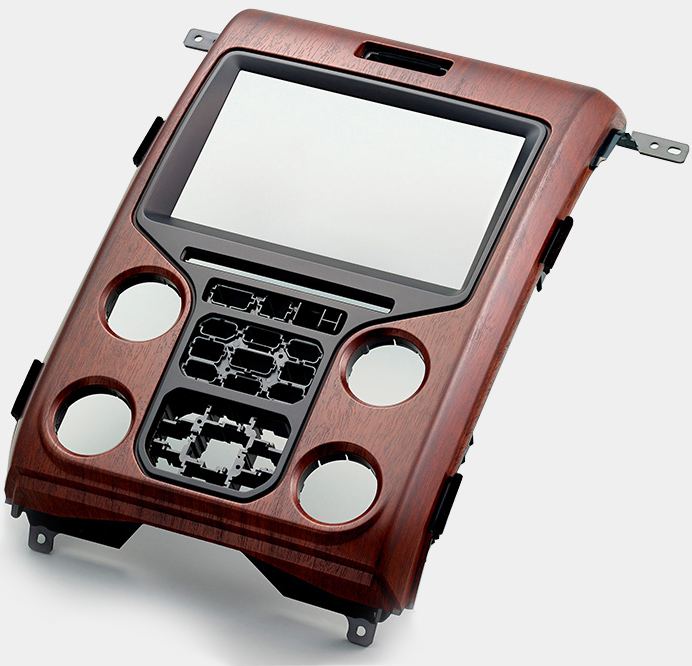
Technical Specification
Printing method for IML Film
Gravure printing, Sink screen printing (Roll format and Sheet format)
Carrier film material (The film remaining on top)
PET, PC, PMMA+ABS (laminated)
Applicable resin for injection molding
ABS, PA, PC, PC/ABS, PET, PMMA, etc…
Surface finish (Gloss level)
High gloss (Piano black), Mid matte (65), Low matte (25), Alpha-matte (tactile texture)
Surface finish (VM = Vacuum Metallization)
ALVM (Aluminum VM), LCVM (Low Conductive VM), Chrome VM
Surface function
Hard Coat (Scratch resistance), UV shielding, Anti finger print, Anti reflection
Other function
IR transmittance ink, Low conductive ink (RF performance)
Q & A
How to get a quotation and DFM (Design for Manufacturing) report for IMD or IML parts?
Based on your product requirement for geometry, CMF finish, project volume and supply chain, Nissha will offer best solution.
Please share with us: project summary, 3D CAD data, artwork, supply chain preference. Then we will provide quotation and DFM study with your best supply chain shortly.
If that information is not available yet, don’t worry. Please provide us the preliminary information for your product, and our sales and engineering team will advise budgetary price and technical feedback.
How to select process, IMD, IML or Heat Transfer….
Based on your product requirements for geometry, CMF finish, project volume and supply chain, Nissha will offer the best solution.
As described in “Comparison between IMD and IML”, geometry and project volume especially would be the key to select either IMD or IML process.
Heat Transfer is a more cost-effective process and no special tooling is required. We can decorate current molding parts, although there is some limitation of available geometry by Heat Transfer process.
Where are IMD or IML products manufactured?
We have manufacturing facilities located globally in US, Mexico, China, Malaysia, Japan, Germany… For our manufacturing location detail, please see here.
Are IML parts OK for outdoor use?
Yes, our IML parts are used for outdoor application. We have several film options depending on customer’s functional requirement. In case of choosing a specific IML film, we can make IML parts which are durable against UV irradiation and chemical resistance.
