In Mold Decoration
IMD = In Mold Decoration is the technology to apply versatile CMF finish onto 3D geometry plastic surface during injection molding.
This technology widely used in consumer electronics, appliance, automotive and medical/healthcare devices, and supports customer to achieve unique CMF finish on mechanical parts with high quality and productivity.
Key benefits
Hard coat protection
Nissha’s UV cured hard coat layer protect surface against scratch, chemical, UV irradiation without secondary process.
Decoration on 3D geometry
Since decoration is applied at the same time of injection molding process, surface decoration follow 3D geometry.
Precise registration
Nissha foil feeding system is managed by optical sensor and +/-0.25mm precise registration is available.
High productivity by roll to roll system
Film printing and IMD molding is managed by roll to roll system. Its production is automated and efficient.
Environmentally friendly
Thin IMD ink is only applied to the area where decoration is needed. Volatile organic compounds can be reduced.
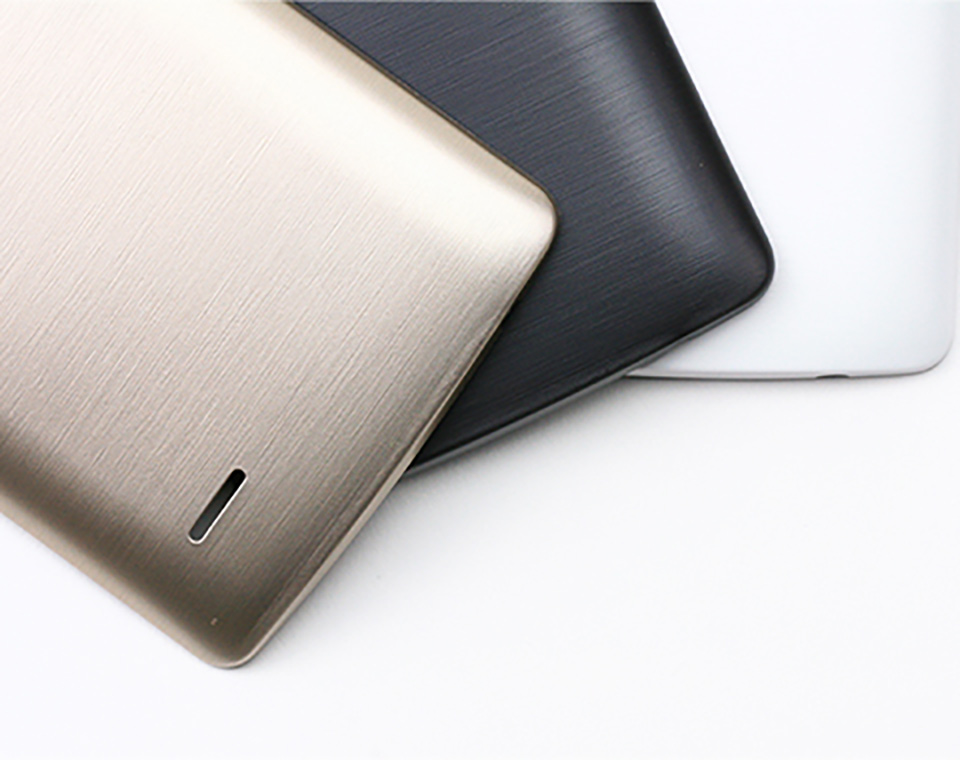
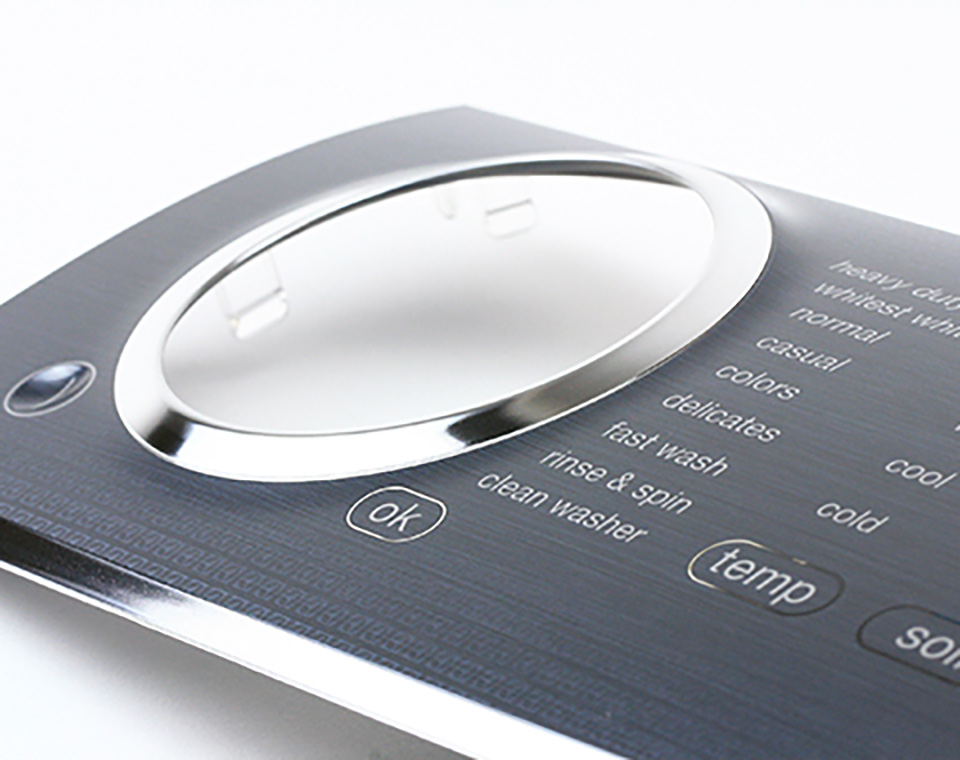
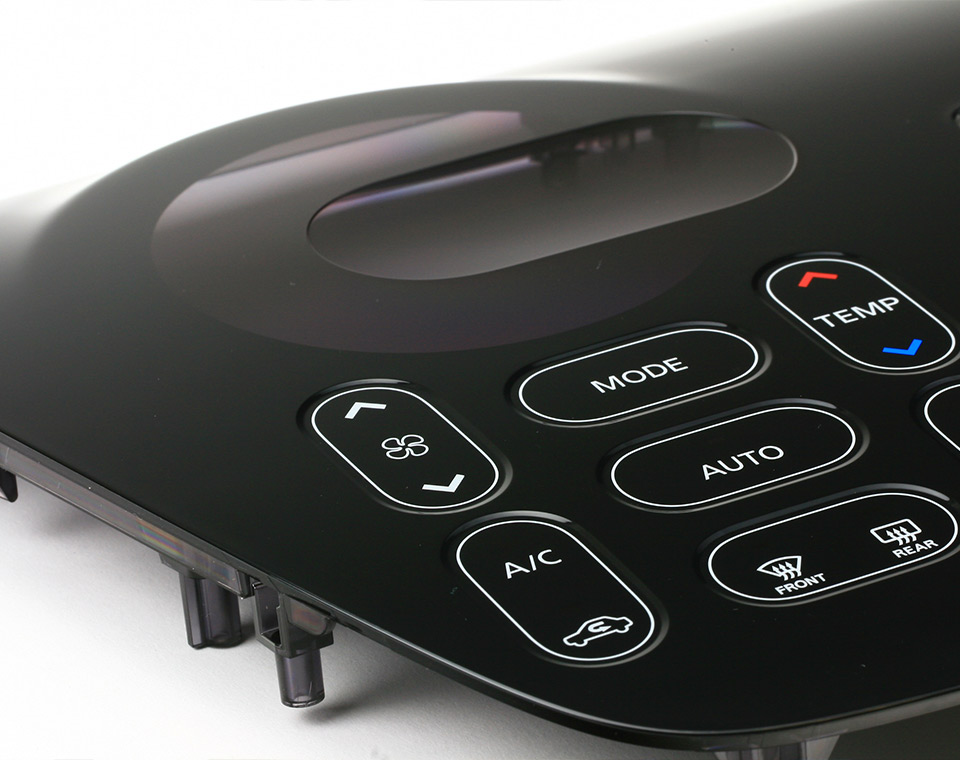
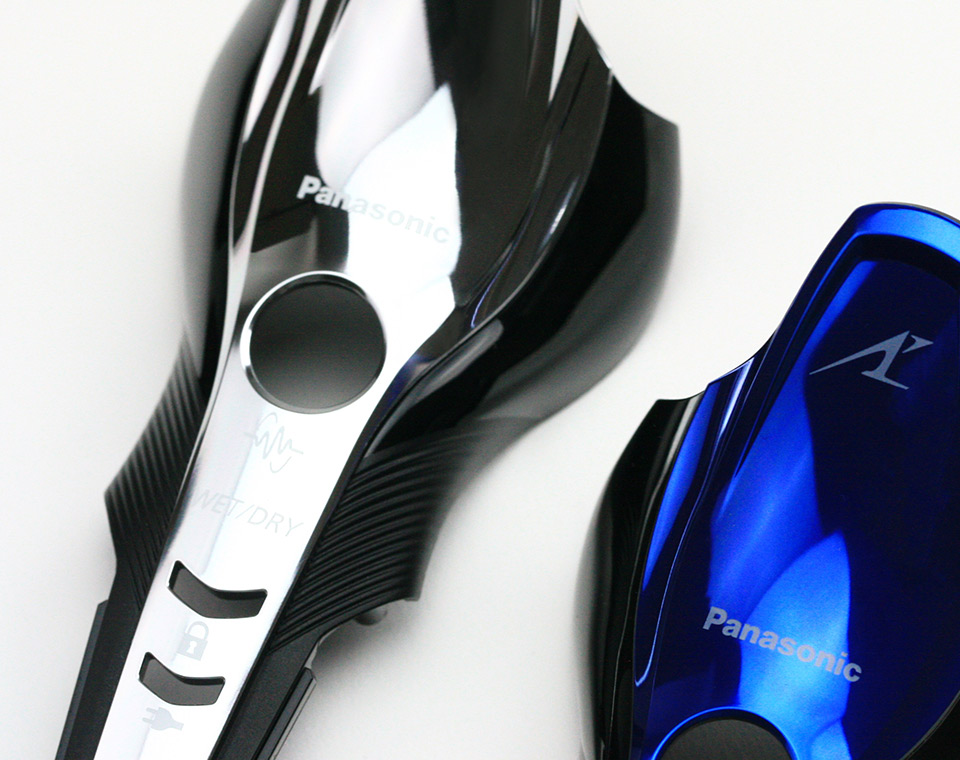
Process
IMD is a simple and productive process. Decoration is done inside of the tooling without any pre / secondary process, and the whole process is managed by a roll to roll system. Decoration is completed, including hard coat protection, with just a single shot molding.
Composition
Process Flow
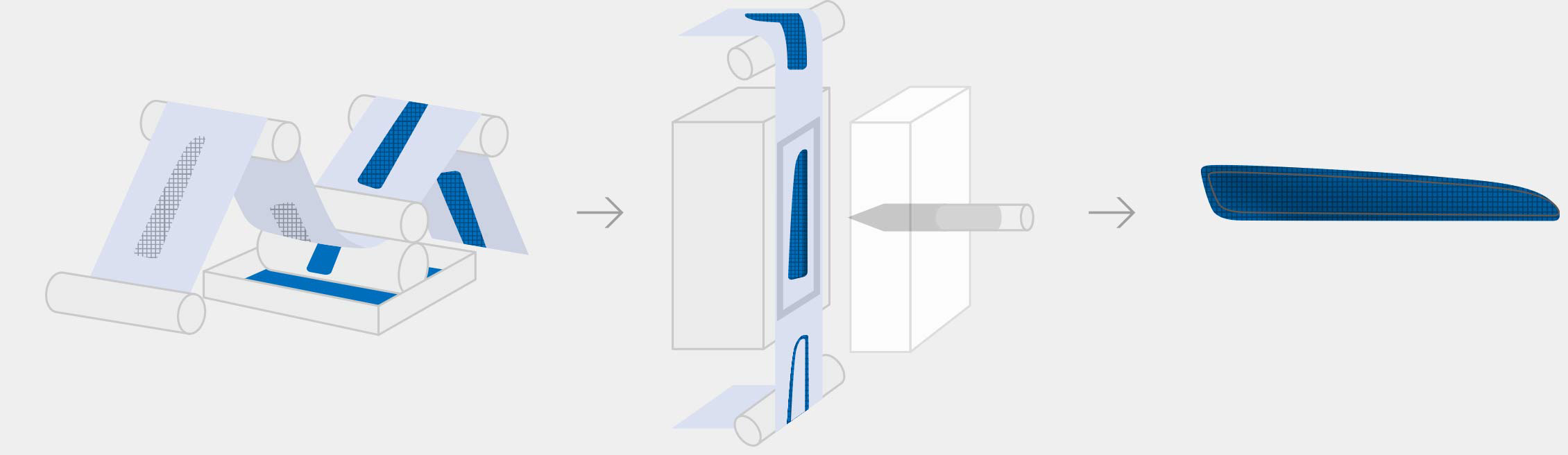
Gravure printing
IMD film is printed by high speed gravure printing process.
7 layers of graphic color (max) plus also hard coat layer and adhesion layer are applied during this printing process.
IMD molding
A foil feeder is installed on the injection machine. IMD film is then fed between the injection molding tool. Optical sensors in the feeder adjust registration of the film, and the ink printed on the film is transferred onto the plastic by the heat and pressure of injection molding.
Product
After injection molding, the result is finished decorated products. No secondary process is necessary.
(In case UV cure HC is applied, there is a UV curing process.)
Versatility of CMF design
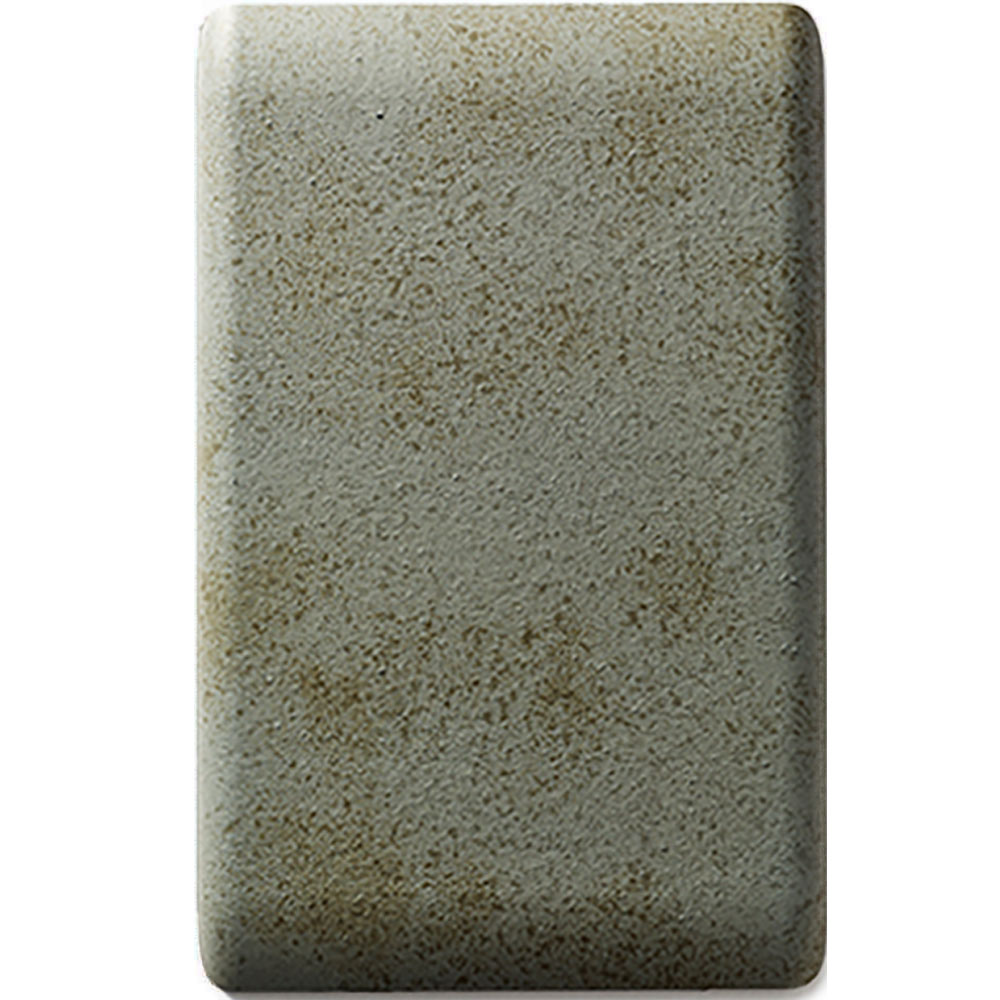
Depth / Multi Layer Effect
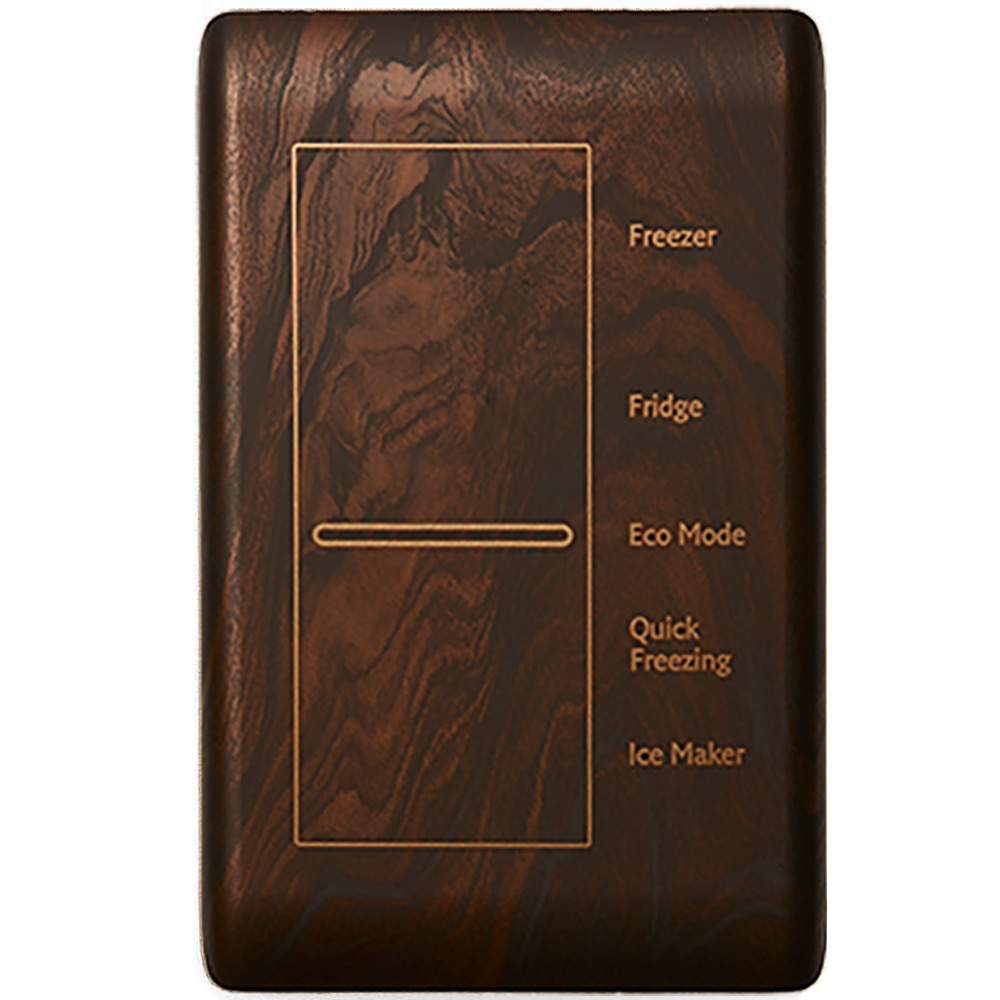
Hidden Til Lit
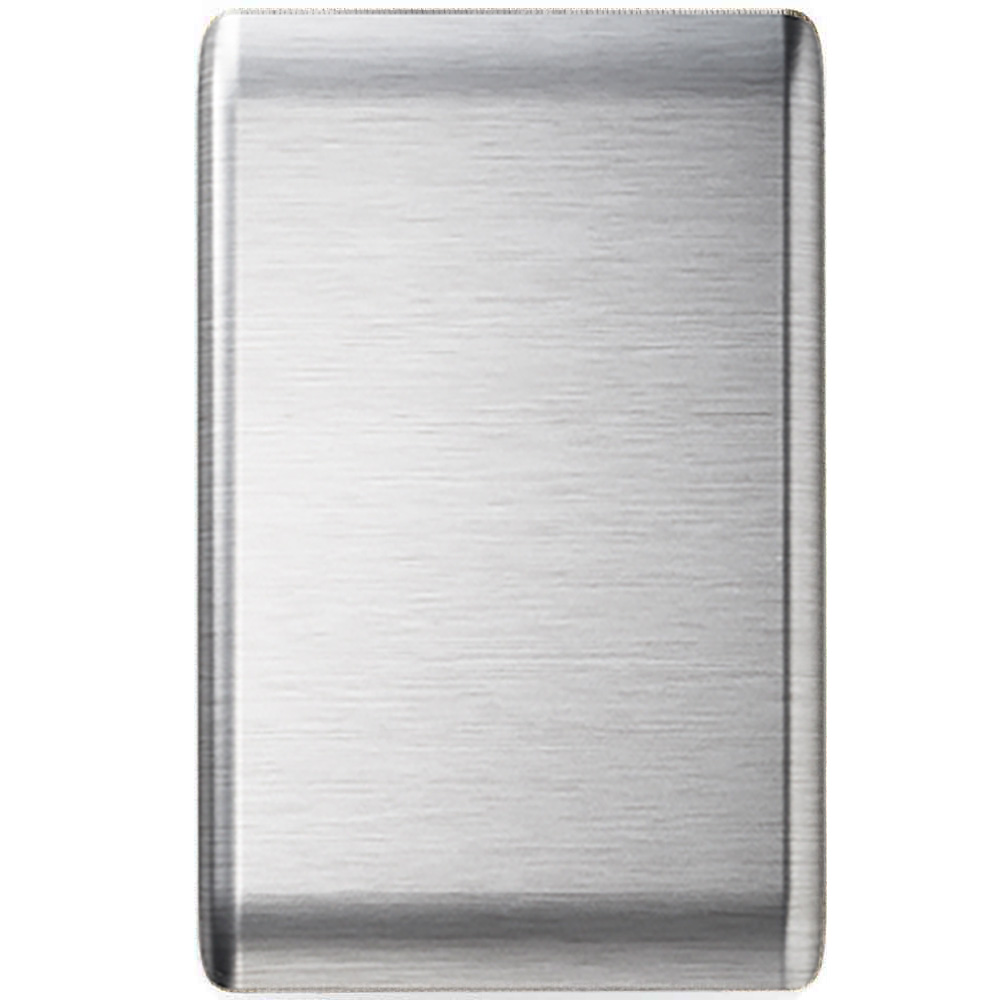
Brushed Hair Line
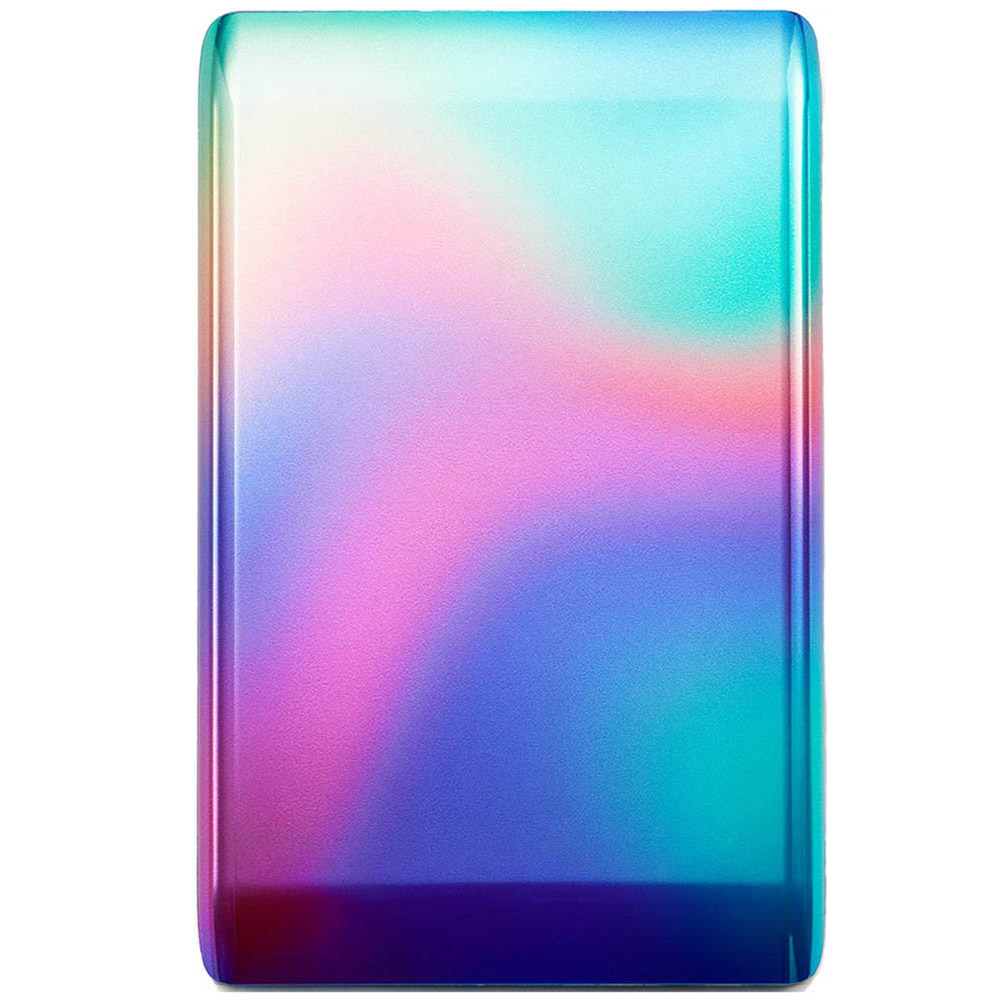
Gradation
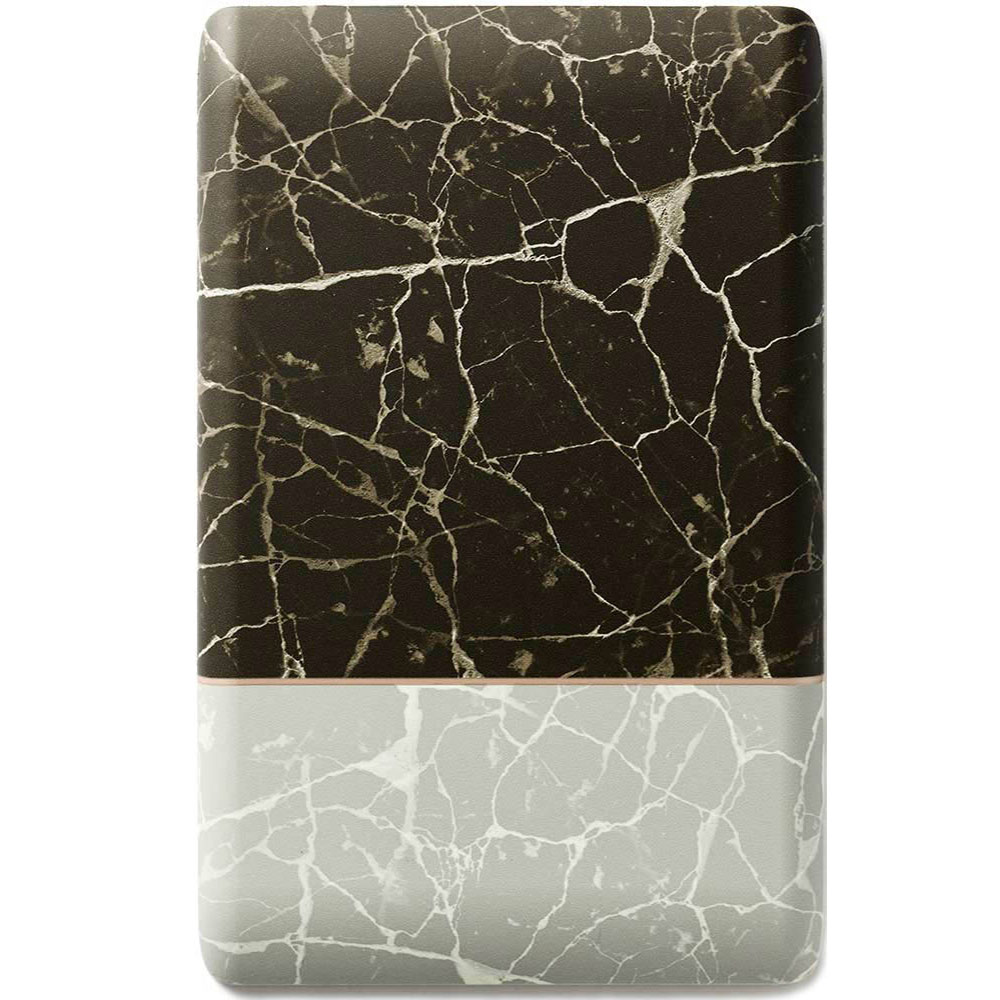
Marble Stone

Wood Grain
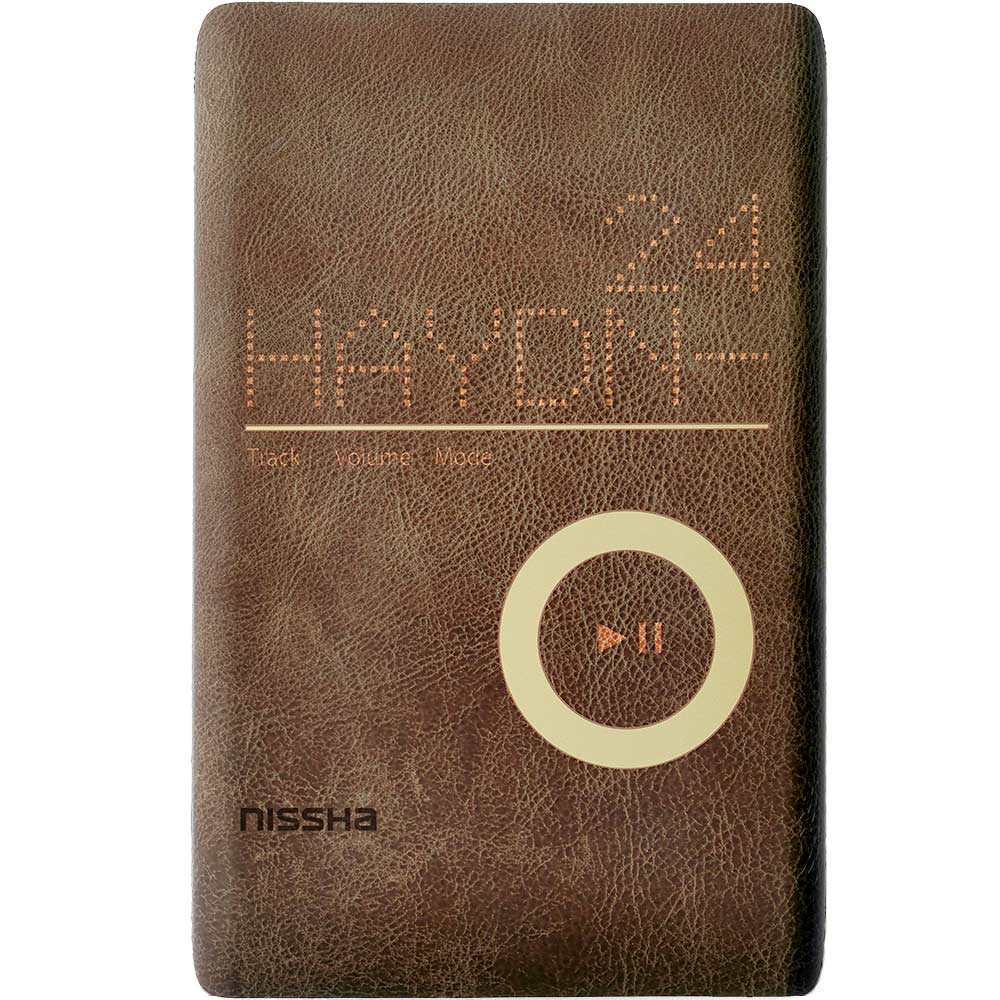
Leather

Fabric Texture
Technical Specification
Printing method for IMD film
Gravure printing, Silk screen printing
Applicable resin for injection molding
ABS, PA, PC, PC/ABS, PET, PMMA, TPU, etc…
Surface finish
(Gloss level)
High gloss (Piano black), Mid matte (65), Low matte (25), Silky touch (10), Soft touch (10)
Surface finish
(VM = Vacuum Metallization)
ALVM (Aluminum VM), LCVM (Low Conductive VM), Chrome VM
Surface function
Hard Coat (Scratch resistance), UV shielding, Anti finger print
Other function
IR transmittance ink, Low conductive ink (RF performance)
Derivative IMD technology
2 sided IMD, 2 shot IMD, Metal insert IMD, DD (deep draw) IMD
Q & A
Is it possible to make prototype samples quickly based on my specific artworks/colors?
Yes. Prior to printing films by mass production, we can provide a quick and easy version of prototyping called a “baby print”. What you need to prepare is basically your artwork (Adobe Illustrator data (.ai) and color specifications (Pantone numbers, reference samples, etc). Any additional information will help to achieve what you envision. Lead time is generally 3-4 weeks.
Is shiny VM (Vacuum Metallization) finish compatible with antenna (RF) performance?
Yes, we have a low conductive vacuum metallization (LCVM) material for our shiny metallic finish. Our LCVM material is used in many products requiring RF performance or touch sensor like mobile phones or appliance UI panels.
What is the difference between IMD and IML?
IMD means In Mold Decoration. IML means In Mold Labeling.
The main difference is in the composition – if the carrier film remains after molding or not. In IMD, the decoration ink is transferred onto the plastic surface and carrier film is released after molding. In IML, the film is remains on the surface after molding.
From a commercial point of view, IMD is cost effective for mid to high-volume production and IML can manage well for small to mid-volume production. From the engineering point of view, IMD is a suitable fit for shallower or mild curvature geometry, while IML can achieve deeper and more complex geometry.
Will Nissha supply IMD parts or IMD film only? What is the supply chain for IMD production?
Based on customer preference or the supply chain needed, we can provide the optimal product format.
We provide IMD molded parts from our molding factory globally – including even sub assembly parts or UI panel with touch sensor module. Also, if customer would like to manage molding in their factory, we can provide IMD film and IMD tooling.
For Nissha’s manufacturing location details, please see here.
